Bread is the most important food in the western world. Each EU citizen consumes an average of 70 kg of bread every year (1).
Bread, like other baked foods, is notoriously perishable and although it is at its best when consumed 'fresh', this condition only lasts a few hours after the product has left the oven.
In fact, mainly during storage and packaging, it undergoes a series of changes that lead to the loss of its organoleptic freshness.
The factors that deteriorate bread during its storage are mainly divided into two groups:
- those attributed to microbial attack, and
- those attributable to physical changes that lead to the progressive firming of the crumb, commonly referred to as 'staling'.
The most common source of microbial deterioration of bread is mould growth.
Less common, but still causing problems in hot weather, is the bacterial spoilage condition known as 'rope' caused by the growth of Bacillus species.
The least common of all types of microbial spoilage in bread is that caused by certain types of yeast.
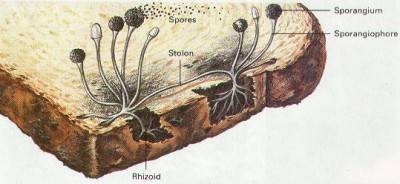
Mould spoilage is due to post-processing contamination. Freshly baked breads are free of mould or mould spores due to their thermal inactivation during the baking process (2).
Bread is contaminated after baking by mould spores in the ambient air during cooling, slicing, packaging and storage.
The environment inside a bakery is not sterile because dry ingredients, especially flour, contain mould spores and flour dust easily spreads in the air.
It is estimated that 1 g of flour contains up to 8000 mould spores. In some bakeries, a similar number of spores are deposited on 1 m2 of surface area every hour (Doerry, 1990).
Production operations such as weighing and mixing ingredients increase the number of moulds in the air.
In larger bakeries where segregation is possible, the flour handling areas are separated from the cooling and packaging area of the finished bread.
The solution.
UV-C ultraviolet irradiation can destroy and inactivate microorganisms such as moulds and bacteria, reducing the risk of contamination and the formation of moulds.
UV-C technology is tested by independent laboratories for its effectiveness in destroying viruses and bacteria, and is commonly used in state-of-the-art, high-tech food industries.
UV-C solutions for the food industry are specifically designed to be installed in the different environments of the food industry, as well as in a bakery.
They are made of stainless steel to ensure compatibility with food production machinery and to guarantee quality and durability.
They are mainly installed on packaging lines, where the product is at greatest risk of post-production contamination. However, the applications are many and include raw material storage and the production lines themselves.
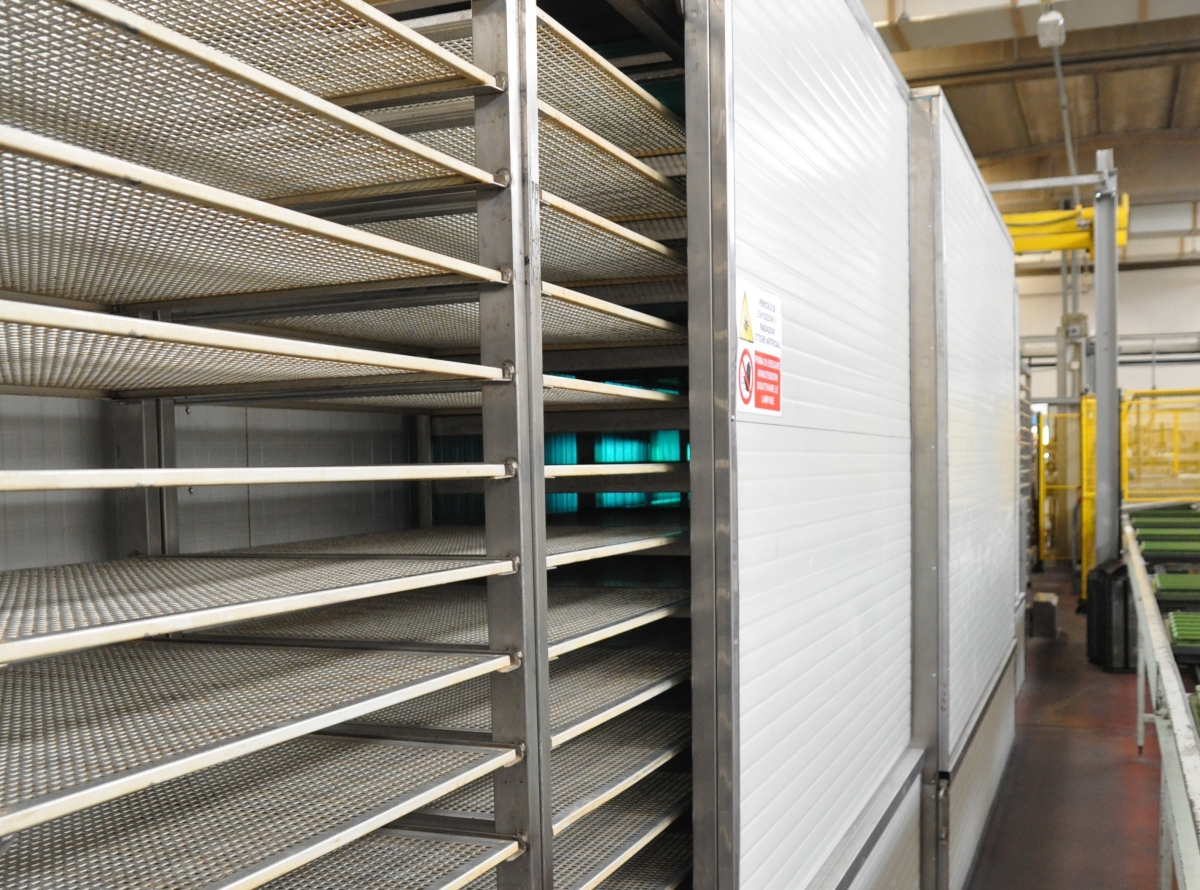
Main benefits of UV-C technology for the food industry.
There are many but some of the most critical:
- Increase the shelf life of the product.
- Reduce consumption of chemical, which would risk altering the organoleptic qualities of the product
- Increase the quality of the finished product, positioning it above competing products that do not use innovative disinfection technology
For the last 35 years at Light Progress we have been designing, developing and producing UV-C solutions for disinfection against viruses, bacteria, pathogens, moulds and other contaminants.
Our FOOD INDUSTRY solutions are designed and manufactured specifically for the food production industry and currently used by hundreds of companies in more than 50 countries worldwide.
Discover our applications for the Food Industry at: https://www.lightprogress.it/en/solutions/industrial-production-disinfection/
1. Source: Italmopa - Associazione Mignai Industriali d'Italia
2. Source: Ponte J. G., Tsen C. C. (1978). Bakery products. In: Beuchat L. R. (ed.), Food and Beverage Mycology. AVI Publishing Co. Westport, CT, USA. Pp. 191-223.